Disadvantages of a Success Story
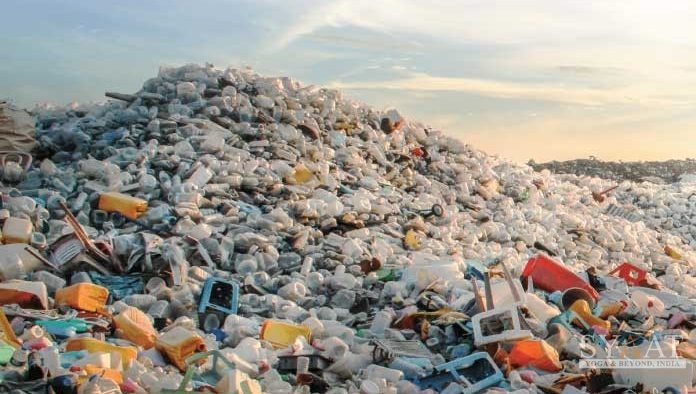
PLASTICS today can be tailor made to suit precisely any type of requirement, just name the type you want golden, silvery, silky,glassy, rubbery, leathery, porcelain or the sort resembling steel, marble, ivory, wood, horm o shellac and you can readily have it. Further, you can make plastic hard or soft, rigid or pliable, tough or gragile, sensitive or resistant to heat, opaque or transparent brittle, bendable or pourable.
With such built in flexibility, it is small wonder that plastics today have emerged as a versatile packing material permitting a multi trade of combinations and effects not possible with traditional materials. In fact, the impact of plastics has been so widespread, especially in the food packaging industry in recent years, that the consumption of plastics in this area alone has increased from 2 million tonnes during 1985-86 to 5.5 million tones in 1988-89.
By their very nature, plastics are exceptionally inert and therefore durable. However, they invariably contain some very reactive components including the residual raw material and solvents, catalyst remnants, antioxidants, plasticizers, stabilizers, lubricants, colourants, surface-active agents, fillers and fungicidal agents. Where direct contact occurs between the packed food stuff and the plastics, it is likely that some of these ingredients present in the plastic will migrate into the food, causing contamination and consequent risk of toxicity to the consumer of the packed food.
To minimize the risk, which may lead to serious disease or even death, most countries have by now formulated guidelines for the manufacture and use of plastic for food packaging applications. The Bureau of Indian Standards(BIS, formerly ISI) too has brought out specifications and positive lists of constituents for plastics commonly used in food packaging such as polythene, polypropylene, polystyrene, PVC nylon etc.
But the saddest part of the success story of plastic food containers in India is that an astonishingly high percentage-98 per cent- of the large number of marketed samples tested (lunch boxes, feeding bottles, water containers etc.) failed to meet American, British and Japanese standards. The failure rate was 53 per cent, when tested for conformity to existing Indian Standards, which are obviously not so strict compared to the US, UK and Japanese standards.
The testing was done in India at the Industrial Toxicology Research Centre in Lucknow during 1983-87. The findings, no doubt, clearly point to the urgent and dire need for strict quality control of all plastic packaging materials made in India for food contact applications.
It must be emphasised that absolute safety of plastic food packaging is not our goal and it never will be because it will always remain an impossible dream “Safe” has therefore been defined as ‘not presenting a socially unacceptable risk’. The assessment of risks can be made more accurately today than in the past, because there have been considerable advances in toxicology as well as analytical techniques.
The advances have shows that the number of chemical substances, many in common use and known to have serious toxic effects, has grown at an alarming rate. There is acute public concern about cancer, for instance, and this has resulted in a demand for all materials to which the public is exposed, to be tested for their cancer producing potential.
In the context of this public concern, it is surely desirable not to permit PVC(Polyvinylchloride) or any of its copolymers for food packaging applications, since the final plastic material is bound to contain varying amounts of vinyl chloride(VC), the basic raw material for this plastic.
VC is well known for its ability to induce a rare and fatal form of liver cancer called angiosarcoma. The BIS prescribes a maximum limit of 1 ppm ( 1 part of VC per million parts of plastic) whereas the FDA(Food and Drug Administration) of the USA permits only a much lower maximum level of 5 ppb(5 parts per billion parts of the finished plastic). In India so for, the facilities for detection of such small amounts simply do not exist in the majority of testing laboratories, which means routine quality control of PVC for food packaging is just not feasible. Under the circumstances, there can be no guarantee of good quality as far as the plastic is concerned for packing food.
The use of PVC in food packaging poses still another problem. It has been found that any adorous additive present in PVC plastic easily migrates to the food packed, adversely affecting taste and flavour. It is also worth nothing that flexible PVC may contain as much as 40 per cent of plasticisers, which can be toxic to mammals. Tricresyl phosphate, for instance, is an exceptionally good plasticiser, but unfortunately it is also extremely toxic. It was traces of this chemical in cooking oil, which crippled for life several people near Dum Dum in Calcutta in 1972. This plasticiser is of course not permitted in food grade plastics. But how would consumers know whether it is present in the plastics they buy for food packaging?
The use of colour in flexible as well as rigid plastic packaging materials is of course another area of concern in india. It has been found that in certain cases, even when the colour layer is not the food contact layer as it lies sandwiched between other layers, colour easily migrates into the packed substance. Needless to say, such coloured plastics are unsuitable for packing foodstuffs, Pharmaceuticals and drinking water.
The highlights the necessity for layers other than the contact layer also to be food grade. It is also desirable to use only the few permitted colourants in food packaging, rather than choosing one from among the many others available.
The FDA (USA) permits the use of inks containing heavy metals on flexible food packaging material, provided the inks are separated from the food by a barrier layer. But US Department of Agriculture oppose this because the usual barrier materials such as films, coatings, and aluminium foil are considered inadequate to protect the food from this inks.
A major drawback in the use of plastic packaging for foods in a tropical country like ours is that migration of the reactive chemicals present in the plastic material into the packed food will increase exponentially with temperature. It has been reported that often the temperature in warehouses reaches as high as 600 C at roof level and the present BIS standards do not take care of this aspect.
With the ever increasing use of plastics in almost every sphere of life, the quantity of plastic waste material is also mounting. Much of this plastic waste is now being melted and remoulded to give recycled plastics. The use of recycled plastics for packing food can be potentially dangerous due to the greater and more serious contamination they can cause.
Fortunately we have in India today a number of manufactures making food grade plastics. But there is no way a consumer can find out which of the marketed containers or packaging is really food grade. As a consumer, I would certainly like manufactures to label the plastics they make as ‘food grade’, after satisfying themselves that the materials do confirm to the standards laid down. To carry conviction with consumers, it is also essential that all plastic intended for food contact applications are certified as food grade by a competent authority.
Consumers in general must abstain from using empty plastic containers originally used to pack commodities other than foods, as well as the cheap trash offered as free gifts with bulk purchases. Some of these are attractive enough to catch the attention or housewives but using them for storing any food may turn out to be disastrous.